For 50 years Eventide has pioneered unprecedented ways to bend, distort, and manipulate sound. To celebrate our 50th anniversary, we'll be highlighting the products that started it all. Here's the first Intelligent Audio Processor!
- Eventide has painstakingly modeled every section of the analog signal chain to recreate the sounds of the original H910.The original H910 was a 100% software-free, analog and digital processor that predated the earliest practical ADC or DSP chips by several years.
- The H910 Harmonizer was the world’s first digital effects processor. With its unique combinations of pitch shifting, modulation and delay, the H910 can be heard on countless ground-breaking works by artists from AC/DC to David Bowie and more. Eventide H910 is available to purchase from the T+S store.
“Ding Dong! The Glitch is Dead”
Eventide H910 Harmonizer Again, the H910 was the first true studio pitch changer. Eventide’s de-glitch circuit was still a few years away, but you got dual outputs, each with short, selectable delay times. May 07, 2010 In 1975, Eventide came out with their first Harmonizer, the H910. Designed by Anthony Agnello (later of Princeton Digital), this was a digital variant of the rotary tape head pitch shifters that I discussed earlier. See full list on sweetwater.com.
The success of the H910 was gratifying, especially considering its limitations; for one thing, you could only do so much with 100 milliseconds of delay! We were already thinking about a new, improved model even as the first H910s shipped. At the time—the mid ‘70s—IC technology was sprinting ahead. The 4k-bit RAM chips in the H910 became ‘old news’ once 16k-bit chips were available. And, by 1977, logic ICs had progressed to doing simple but fast arithmetic, which enabled a host of unheard-of effects.
The H949 benefited from the rapid pace of IC development with improved audio specs and much more. It represented a major advance in the very notion of an effects box and introduced the terms algorithm, random, and micropitch to the audio lexicon. Our marketing message was simple—“more of everything.”
Our ad cheekily called out some of the novel features:
The Glitch’s Tale
The long list of “more of everything” included longer delays, radical new features, and better audio specs. But, for this Flashback, we’ll focus on the ‘devilish pitch change glitch’ that plagued the H910 and the method that we came up with for smiting it.
Why was taming the glitch so important? Didn’t some people love that devilish glitch? Yes, perhaps some did, but most simply tolerated the glitch while appreciating that the H910 opened up a new world of sonic possibilities. Others had the hope that it could be used to help solve a sticky problem: ‘pitchy’ vocals. On that score, it fell short for two reasons. First, it was difficult to dial in small, precise pitch ratios, and second, the random glitch made for hit-or-miss results.
The H949 was the first pitch-change box designed to be a tool for tuning. It had the necessary fine resolution, as well as the ability to analyze audio in real-time and make decisions that avoided audible glitches. Engineers welcomed this new capability and found that while monitoring a problematic track, they could twist the big knob—at the right time and by just the right amount—to bring a wandering pitch in tune. Bear in mind that, in 1979, autotune was still more than a decade away. This process was a hands-on, real-time performance. Engineers discovered that the H949 could bail them out. Here’s a case in point:
The path to solving the glitch problem took a number of twists and turns. If you’re game, come along with us as we travel Nerd Boulevard! Alternatively, flash forward to Flashback 7.2 for a deep dive into the H949’s many groundbreaking features.
Why a Glitch?
Let’s explain what caused those devilish glitches in the first place. The H910 was built with the earliest ICs—simple logic gates that could do little more than calculate a couple of memory addresses for each audio sample. It did its best to ‘smooth over’ the discontinuity that occurs when a pitch changer’s delay is forced to suddenly ‘jump’ by several milliseconds when the delay either gets to zero (increasing pitch) or becomes too long (decreasing pitch). The H910 employed essentially the same method as human tape editors who used razor blades and a cutting block to splice tape at a 45-degree angle. The audio segments would, in essence, crossfade. Rather than risking a hard splice (and possible loud ‘click’), the crossfade smooths over any discontinuity. And yet, while the H910 employed the same crossfade splicing method as editing tape, there are two significant differences:
- Over the course of a 3-minute song, there might be as many as a dozen tape edits/splices. A real-time pitch changer, depending on pitch ratio, may make hundreds of splices over the same period.
- The tape editor can listen to the audio and ‘decide’ where to splice. The H910 could neither listen nor decide. Its splicing method was aesthetically agnostic with unsurprisingly uneven results.
We called the artifact that resulted from the pitch changer’s random crossfading the glitch. The experience with tape editing made it clear that the way to handle the glitching problem was to do what a human tape editor does: Find ‘good’ places to splice. If only the electronics could compare two portions of the signal so that, when a splice was necessary, it would occur between two points on the track that were similar to each other. Finding such a similarity uses a process called autocorrelation. So, the ‘solution’ was rather clear. In fact, across the pond, a couple of ex-aerospace engineers, Mark Crabtree and Stuart Nevison at AMX, reportedly had arrived at the same ‘bleeding obvious’ conclusion.
While, theoretically, autocorrelation was the way to go, the practical reality was that until the late ‘70s, ICs weren’t up to the task of ‘processing’ audio in real-time. Autocorrelation of a real-time audio signal requires many thousands of multiplication operations per second. ICs capable of doing this arithmetic quickly were still years away. So, we decided to hedge our bets by providing our new model Harmonizer® special effects unit with the option to select one of two methods for pitch change. Anticipating the day that ICs would be up to the task of real-time analysis and decision making, we designed the H949 with the ability to add new, ‘intelligent’ hardware that could make smart splicing possible.
The Algorithms
The H949 gave the user two methods to mitigate glitching, which we dubbed ‘algorithms.’ The User Manual introduced the word ‘algorithm’ to the audio community, defining it as “a precise, describable process which acts upon or modifies inputs in a specific manner.”
Algorithm #1 was new, yet simple. It created slow, gentle crossfading that eliminated hard glitches, but caused a ‘swimming’ effect at extreme pitch ratios. When the first H949s shipped, Algorithm #2 was similar to the H910’s method and had similar, random results. The plan was to offer a hardware upgrade for Algorithm #2 when newer, faster ICs would make intelligent splicing, and hence de-glitching, practical.
Intelligent electronics?
Eliminating the glitch required more than just the intelligence for signal analysis and decision making; it also had to perform the complicated signal memory addressing required for de-glitching, and to make those computations at audio rates.
Real-Time Audio: It’s a Matter of Time
Early ICs were not only vastly simpler than today’s devices, but also much, much slower. Real-time digital audio has a fundamental constraint in that processing has to be completed on a sample-to-sample basis. Assuming a 50 kHz sample rate, the analog to digital converter spits out a new sample every 20 microseconds and the processing must keep up with this never-ending flood of samples, forever.
Today, processing audio in real-time is no longer an issue, and in fact, it hasn’t been for about 3 decades. The microprocessor in your cell phone can run audio algorithms far more complex than that in the H949 while it’s playing video games. But in the early IC era, dedicated logic circuits were needed to get the simplest tasks done, e.g., to perform a couple of additions to calculate an address to keep up with real-time.
Bit Slice ALU for Addressing Memory
Enter Advanced Micro Devices, nowadays a credible competitor to Intel. The first Arithmetic Logic Unit (ALU) capable of computing memory addresses fast enough to keep up with real-time audio was their ‘bit slice’ AM2901. What’s ‘bit slice’? Each chip could add, subtract, and store only 4-bit data (a “nibble”) but multiple chips could be combined to perform simple arithmetic on a digital number of any length. To address the 16K memory of the H949, addresses had to be at least 14 bits long, so our ALU used four bit-slice chips to create a 16-bit number. Here’s a photo of the four chips that were the heart of the ALU:
Microcode
The high-speed ALU of the H949 made it possible to compute—hold on to your hats—16 instructions to handle splicing and 16 memory addresses in every 20-microsecond sample period! In other words, the ALU’s entire ‘software’ program consisted of a total of 16 lines of ‘code.’ Here’s a sample of Tony Agnello's handwritten instructions for handling splices:
With this fast addressing capability, the H949 could offer new features like random delay, reversed pitch change, micropitch, and, if only some intelligence could be added, smart splicing. Adding the intelligence necessary to de-glitch seemed years away…
...But then we got lucky!
The Mystery Chip
Here’s the H949 with its top board flipped up:
Take a close look at the add-on circuit board, the LU-618; dubbed the Lupine Board:
The Lupine board harbored a secret. Note that the part numbers were erased on the two big chips:
Why the mystery? Well, as mentioned, we had gotten lucky and we didn’t want our competitors to ‘share’ our luck. Thanks to the military’s need for ‘impossibly’ fast processing, some clever souls at a company called Reticon came up with a way to use special analog CCDs (Charge Coupled Devices) to analyze signals in real-time nearly a decade before the first DSP chips were available! This obscure and one-off technical advance made it possible to create what was arguably audio’s first intelligent, real-time audio processor. The LU-618* ‘de-glitch’ board with the Reticon chip was offered as an option ($740 in 1979 ≈ $3,000 today!) and well worth the bucks when one considers the cost of studio time—or if the band had left the studio, the impossibility—to re-take pitchy vocals.
The H949: At the Dawn of Intelligent Electronics
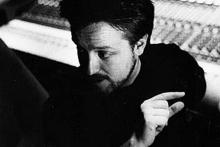
The H949 was at the forefront of smart electronics. It was able to analyze audio in real-time and make decisions based on that analysis. It was used to create new sounds and to correct pitchy tracks. We’ll close with the original draft of our initial H949 magazine ad. Can you find the typo?
Here’s the data sheet for the Reticon chip, the charge-coupled (switched analog) correlator IC designed for military applications (radar). This was the missing piece enabling the design of the first de-glitched Harmonizer. The H949 used autocorrelation to analyze the audio in real-time and, based on that analysis, intelligently select the splice points.
In 1979 the H949 appeared at the Audio Engineering Society (AES) Convention in NYC, here's the original press release:
*Why LU-618? Heather Wood, late of Dolby, was our marketing department at the time and a Monty Python fan, as were we all. When the subject of selling this upgrade was being discussed, she dubbed it the “Lupine” board and thus it became. The origin of the numerical suffix is lost to history.
Learn more from the pros:
In case you missed our first flashbacks:
Try the H949 Harmonizer Plug-in
Popularized by Jimmy Page (as the only piece of digital gear to grace his rig) and cherished by Suzanne Ciani, the H949’s full feature set is authentically emulated in this multi-effect plug-in. From basic engineering and sound sculpting tasks to demonic space robot creations; H949 is built to inspire. Try a free demo
We love Eventide and their gear, though we’ve stopped servicing some of the early models. Here’s a partial history of that landmark company, with typical costs for the models that we service.
Service costs for the Instant Phaser, Instant Flanger, and Omnipressor can vary. Faulty switch assemblies can add expense, and Omnipressors often have faulty meters, which increases repair cost. (The switches are an unusual type that are no longer made, but we have a good stock of new and used replacements.) We stock all the parts for these units, including the Reticon CCD chips in the Flanger and the dbx modules in the Omnipressor. These are valuable units, well worth the cost of servicing. Please note that all declined Eventide repairs are subject to a testing and evaluation fee.
There were other late 70’s products. The Monstermat was not so successful scheme to improve the sound quality of radio station cart machines. Better received was the BD955 broadcast obscenity delay, which allowed the producer or engineer of a talk show to mute the words telephone callers without interrupting the program. The first version used 160 RAM chips!
Again, the H910 was the first true studio pitch changer. Eventide’s de-glitch circuit was still a few years away, but you got dual outputs, each with short, selectable delay times. The dbx type II noise reduction cards on the input and outputs allowed a whole 90 db of dynamic range. Though we no longer service the H910, we stock many of its original parts.
I believe that the Eventide H949 Harmonizer hit the market in 1980. Its many improvements over the H910 included “micro” pitch change mode, two pitch change algorithms (neither sounded perfect, but at least the user had a choice), a basic flange function, up to .393 seconds of delay, and “Reverse” mode, which played a stored sample backwards.
Units with serial numbers above 1606 could be fitted with the optional “Lupine” LU618, the world’s first degitch circuit for pitch change. (Early pitch change circuits “spliced” the waveform, with additional splices at extended pitch change settings. This electronic splicing produced periodic clicks. The algorithm on the Lupine card (whose name came from a Monty Python sketch) selected splice points at equal voltage levels, greatly reducing pitch change artifacts.) An H949 with a deglitch card will be marked “option: ALG-3” on its serial number badge.
Another interesting Harmonizer option was the HK940, a two octave keyboard for external control of the H910 and H949. Few of these units survive — if you own one, you’re quite fortunate! For a cool trip down memory lane, check out this original H949 sales brochure. As with the H910, dbx type II cards were used to increase dynamic range. We no longer service H949’s, but stock many hard to find parts.
Eventide H910 Harmonizer Plug-in Suite
As with the H910, dbx type II cards were used to increase dynamic range. Like the H910, we no longer service H949’s, but stock many hard to find parts.
This brings us to the famous Eventide H3000 and H3500. These are true industry standards, seen in all world class studios. Their hundreds of effects algorithms and 600+ available presets provide a wide variety of effects including true stereo pitch shift, pitch-correcting diatonic pitch shift, linear-predictive vocoder, six voice polyphonic synth, and a 19 waveform LFO function generator with full control. The multi-shift algorithm allows six octave pitch shift. Other programs include ultra-tap delay, instant phaser, swept comb filter, and multi-band delay. The LFO offers 19 periodic or triggered waveforms, with pink and white noise assignable to most effects parameters. The D/FX added new algorithms and presets, including a range of Stevie Vai settings. Both models have comprehensive MIDI implementation.
We service all versions of the H3000 and H3500 and can update the program chip sets. Typical service cost is $680.00. This is a labor intensive servicing that includes power supply recap, cleaning any intermittent soft key switches, power supply connector replacement and upgrade, replacement of the NVRAM battery backup IC, cleaning the inside window of the alphanumeric display, internal adjustment of display brightness (if needed), other minor repairs that may be needed, and calibration of the offset and distortion trims. Upon completion, we do a complete 108 point check out of the analog and digital sections using Eventide’s proprietary H3000 test software, replace any missing or damaged chassis screws, and use a paint pen to touch up scratches in the black areas. For users in areas outside of North America, we have a small quantity of alternate version power transformers that are optimized for 50 Hz. power.
Eventide H910 Plugin
Note: in recent years many H3000’s have come to us with dead power supplies, sometimes with customer comments about smoke from the motherboard and burning smells. These problems are nearly always caused by shorted capacitors, which can cause additional failures in the power supply circuits. In these cases repair and testing can be very time consuming because the motherboards have dozens of capacitors in parallel, there’s no easy way of individually testing them, and often many (or most) need to be replaced. These problems can always be repaired, but additional cost is often $200-$250.